Engineered quartz. Description
Reviews
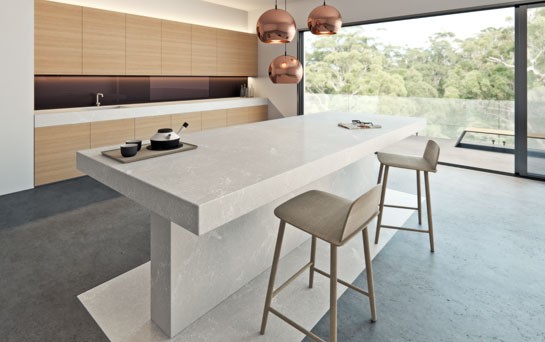
Engineered quartz is a kind of engineered stone made of natural quartz sand with addition of polymer resins and pigment dyes.
Engineered quartz is manufactured as plates, which are usually called slabs.
Composition and features of engineered quartz
determine the following formula:
- 92-95% of quartz chippings and silica powder,
- 5-7% of synthetic resins,
- 1 % of color pigment.
Resins act as a bonding agent while pigment dyes paint the mass with the necessary colors. Engineered quartz’s hardness is comparable to granite because of high content of natural quartz. Stone-cutting, polishing, and grinding machines and other equipment is needed to manufacture products of engineered quartz just as it is needed to process hard natural minerals and rocks.
Engineered quartz’s resistance to mechanical damage and wear resistance is not inferior to granite.
Functionality of items made of engineered quartz is notably higher when compared to granite, marble and other natural stones. The secret is in complete absence of pores, small cracks and voids invisible to the eye, characteristic of all natural stones. Homogenous and nonporous structure of engineered quartz is impervious to dirt, dyes and moisture, which prevents development of microorganisms and mildew.
Items made of engineered quartz, as opposed to marble, granite, and travertine do not need special pastes for being cared for. All contaminations and stains are easy to remove with a sponge and nonabrasive detergent.
Surface of engineered quartz boasts noble natural shine of natural stone.
Manufacturing method of engineered quartz
Chopped gangue quartz is the main component for production of engineered quartz. Quartz chippings are washed, dried and sorted by fraction depending on their size.
In order to obtain a homogenous material without microvoids and pores, chippings are mixed with quartz powder. After adding pigment dyes and resin, the resulting mixture undergoes vibration compaction, next, through exposure to high temperature, the resin polymerizes. Cooled down and hardened slab is then sent for sizing, after which it is being grinded and polished.
All slabs undergo an inspection to detect manufacturing defects.
Factory polishing of slabs can result in matt, semiglossy, and glossy surfaces to them. There are also collections with relief surface of slabs, ornamental design and patterns.
By experimenting with the size of the chippings and different pigment additives, manufacturers of engineered quartz obtain various colors and decors of this material. Interesting results are obtained by using particles of natural stone (e.g., agate, granite, and marble), brass, blue malachite, mother of pearl, mirrors, tinted glass. Color palette, complying with modern design tendencies, is an important competitive advantage of certain trademark.
Field of use of engineered quartz
Engineered quartz became a popular material for producing tabletops and as a lining material as well. Quartz slabs are used for lining hygiene facilities in residential and public buildings, for designing halls and showrooms, offices, and subway stations, hotels and restaurants. Durability and extraordinary wear resistance of engineered quartz enable its usage for lining floors and steps in airports and stations.
Kitchen tabletops and islands with integrated quartz wash basins, bar counters, window sills, and floors are the most popular items to be manufactured from engineered quartz.
From the design point of view, engineered quartz is as attractive and beautiful as natural stones like marble, granite, and travertine. Oftentimes engineered quartz’s decors are so perfect that it is visually indistinguishable from natural stone.
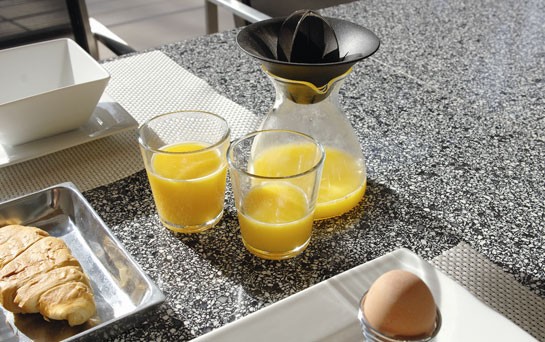
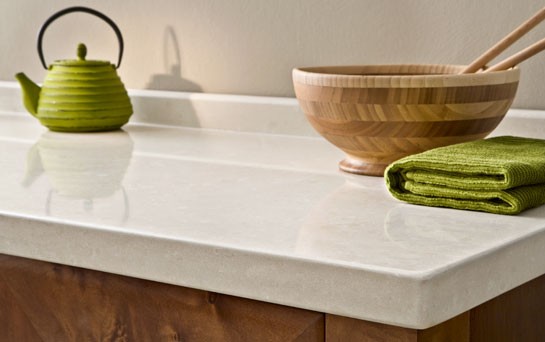